About Us
Producing the world’s leading products with cutting-edge tech & tools
We’re looking for team players who know how to take charge of business-related challenges and keep us running smoothly. Working behind the scenes in our manufacturing plants using the latest production technology and equipment, Plant Technicians are vital to the success of our business at P&G.
Why Join Us Being a Plant Technician Brands & Products Our Facility
Hedley Avenue, West Thurrock, Essex RM20 4AL. Chafford Hundred and Grays mainline stations (C2C train line) are nearest to the site along with several bus routes.
Why Join Us
Starting a career at P&G London Plant will provide you with the skills and resources needed to succeed. You will learn technical skills, business leadership, decision-making, teamwork, safety and ownership. You will learn all this while getting paid competitively from Day 1.
Advancement
At P&G London Plant we value and invest in our people. We have a clear pay and progression system which enables you to advance based on your performance and newly-acquired skills. You will work with passionate people and receive both formal training and daily mentoring from your colleagues and manager.
Training Development | Career Path
Leading Brands & Innovation
At London Plant we produce some of the most iconic P&G brands - Fairy, Bold, Ariel, Daz. At the same time we always strive to be at the forefront of innovation and are currently in the process of growing our production operations for one of our newest brands - Lenor Unstoppables Beads. This makes it an exciting time for technicians to join our business and contribute to the growth of our business.
Culture
We embrace a culture of continuous coaching which means in your role with us you will work with passionate people and receive both formal training as well as day-to-day mentoring from your manager. Simultaneously, we offer a dynamic and respectful work environment where employees are at the core of everything we do. We value every individual and encourage initiatives, promoting agility and work-life balance.
Benefits
We love that everyone is different and understand that, what is most important to you now, might change over the various stages of life. We offer a range of benefits and plans meeting your needs now and in the future. Therefore, we take very seriously our commitment to the compensation and benefits package we offer to our employees. We regularly benchmark our offerings against top peer companies to ensure they remain industry competitive.
Benefit Programs & Compensation | Facility Offerings
Awards & Recognitions
Top 20 Best Places to Work in the UK
Top Companies for Executive Women and Working Dads
Grocer Gold Awards - Branded Supplier of the Year 2017
Top 10 - Top Company for Female Executives & Multicultural Women
Being a plant technician
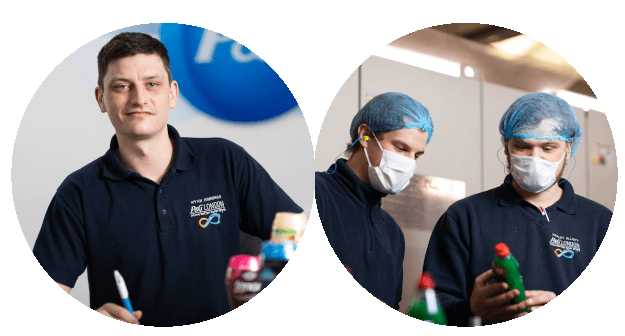
As a technician, you’ll work on a team responsible for keeping production flowing, meeting performance goals, and maintaining the high level of quality that consumers expect from our products.
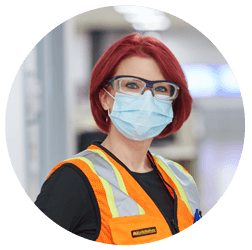
Being involved in making P&G products safe, reliable and exceptional in quality is an amazing feeling.
MEGAN
PLANT TECHNICIAN
What does it take to join our team?
Our plant operates 24/7 and technicians work 12 hours per day in various shift rotations including a single straight shift to working two rotating shifts. Length of work shifts or the rotation schedule can change occasionally and employees can be required to work additional days in the form of overtime.
Also this can be a physically demanding job so you may need to be able to lift heavy loads, use stairs, ladders and platforms, move freely, enter and work in confined spaces, and stand on concrete floors for an extended period of time.
Brands and Products
Our winning products and leading brands are all about innovation – in many forms, from our technology and tools to our work processes to the change we inspire. No matter your role with us, you’ll be part of something impactful and important that makes a difference.
Fairy
Production at London Plant started with fairy household soap, with Fairy Liquid starting production in 1937 and Laundry Detergents in 1947. At the start of the COVID-19 pandemic plant technicians stepped-up to meet the increased demand for Fairy Liquid. And they could do this with confidence as P&G puts so much emphasis on their health and safety. Precautions included enforcing strict social-distancing rules on site to keep employees separated at the plant entrance, taking employees' temperatures, and separating employees to prevent departments from mixing and potential spread of the disease.
Ariel
At London Plant we have been producing laundry detergent for more than 80 years, and Ariel is one of the most important brands we produced at the plant. Our technicians use the latest technologies for the making, packing and shipping of thousands of boxes every day, to the UK and beyond. They play, therefore, a key role in bringing a confident smile on parents’ faces when the dirty clothes of their children reach the washing machine, and they just add Ariel.
Our Facility
We’re located in a state-of-the-art facility, where P&G engineers and plant technicians work together to design and utilize the latest technology to allow our manufacturing plants to produce the highest quality products at optimum production rates.
Innovation of Facility & Machinery
In an ever-evolving world the force of change is unavoidable and tackling this head on is a competitive advantage for P&G. That is why we are constantly looking at applying and developing technology to improve all areas including safety, product quality and sustainability.
Seemingly small changes are amplified onto a massive scale in a 24/7 manufacturing operation and the opportunity to make a difference is huge. To handle the increasing complexity of changes we need talented teams to effectively plan, execute and support the constant marginal improvements in every area of the supply chain.
Importance of Safety
At P&G safety is at the forefront of everything we do and it is also built into the core of the company. Nothing we do is worth getting hurt for, and Health & Safety can and should be managed. The safety culture of a site is very important, and this starts with each individual. We expect those working for us to take safety seriously and play an active part in creating a positive and safe environment for everyone at the plant.
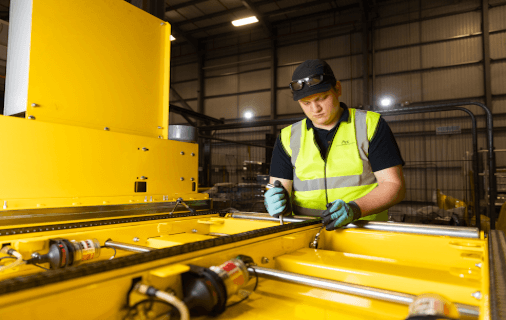
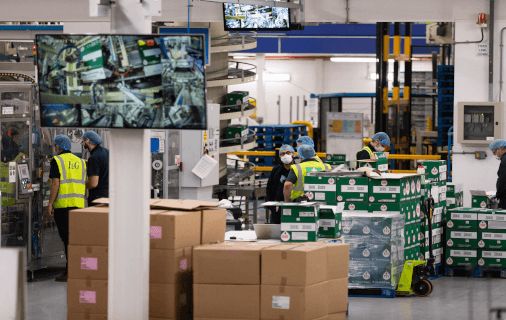